Tighter isn’t always better ….. the impact of compression failures.
- Nexeya Canada
- Feb 19, 2021
- 2 min read
During the fabrication of cables and harnesses there are a number of automated production steps and inspection points that are implemented to ensure quality. From automated stripping and crimping to electrical testing, proper techniques and protocols are paramount to manufacturing a quality product.
Once a quality product leaves the assembly line it takes effort to keep it in good shape. There are a number of factors that can implement the performance of a cable. Shipping and handling can introduce issues, temperature, moisture, vibration, they all have an impact.
Many of these inputs can be controlled through design and packaging, some require more due diligence on the part of the user. Some potential failure inputs, during the installation of a cable include; not respecting the appropriate radius during harness routing, over/under tightening connectors, laying the harness across a sharp feature. The majority of these input will result in mechanical damage to the harness, some visible immediately, others over time.
One failure mode, that is more common than you may think, maybe difficult to notice and may even be the root cause of intermittent failures, is binding or clamping wires or harnesses too tightly. This is an innocent and easy error for an installer to introduce into a system.
This failure, known as a compression failure.

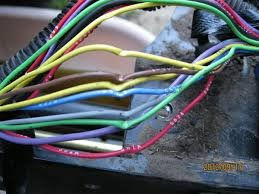
In the most basic sense, the two components of a wire are the inner conductive core and the outer protective (plastic) covering (insulator).
When wires are compressed during installation, as in the photo, the plastic covering deforms. This deformation reduces the wall thickness of the protective covering and therefore reduces the insulative properties of the wire.
These failures can be introduced when using cable ties, clamps, when harnesses are forced through openings or between components. In many cases properly selected clamps – as in this photo, can be used to prevent overtightening and still provide the security desired.

The same Nexeya harness analyzers utilised in the manufacturing of cables and harnesses can be utilised to validate cables and harnesses during and after the installation process. This technique is used by many of our customers, specifically in the aerospace and aviation markets, rail and rolling stock and medical equipment manufacturing.
For more information please contact us at NexeyaCanada@Nexeya.com for more information.
Comments